What Is PLA? Everything You Need To Know
Have you been searching for an alternative to petroleum-based plastics and packaging? Today’s market is increasingly moving toward biodegradable and eco-friendly products made from renewable resources.
PLA film products have swiftly become one of the most popular biodegradable and environmentally-friendly options on the market. A 2017 study found that replacing petroleum-based plastics with bio-based plastics could reduce industrial greenhouse gas emissions by 25%.
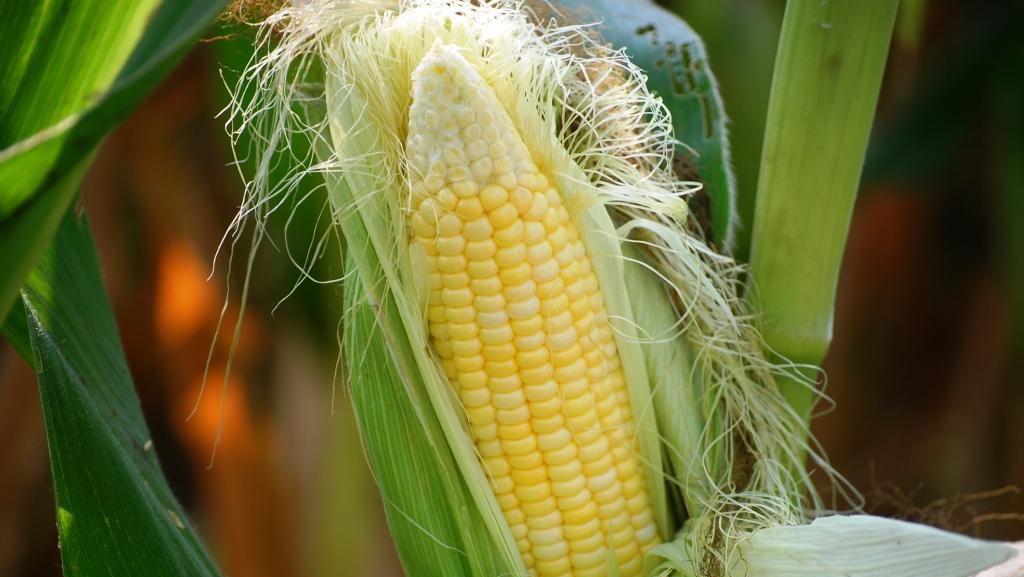
What is PLA?
PLA, or polylactic acid, is produced from any fermentable sugar. Most PLA is made from corn because corn is one of the cheapest and most available sugars globally. However, sugarcane, tapioca root, cassava, and sugar beet pulp are other options.
Like most things chemistry-related, the process of creating PLA from corn is quite complicated. However, it can be explained in a few straightforward steps.
How are PLA products made?
The basic steps to create polylactic acid from corn are as follows:
1. First corn starch must be converted into sugar through a mechanical process called wet milling. Wet milling separates the starch from the kernels. Acid or enzymes are added once these components are separated. Then, they’re heated to convert the starch into dextrose (aka sugar).
2. Next, the dextrose is fermented. One of the most common fermentation methods involves adding Lactobacillus bacteria to the dextrose. This, in turn, creates lactic acid.
3. The lactic acid is then converted into lactide, a ring-form dimer of lactic acid. These lactide molecules bond together to create polymers.
4. The result of the polymerization is small pieces of raw material polylactic acid plastic which can be converted into an array of PLA plastic products.
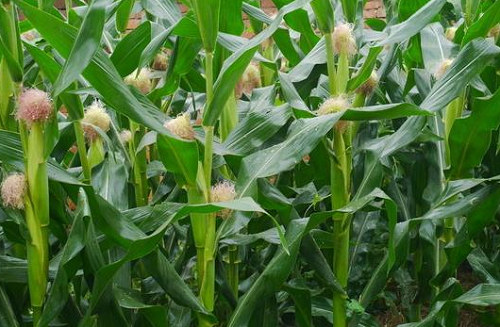
What are the benefits of PLA products?
PLA requires 65% less energy to produce than traditional, petroleum-based plastics. It also emits 68% fewer greenhouse gases. And that’s not all:
The environmental benefits:
Comparable to PET plastics – More than 95% of the world’s plastics are created from natural gas or crude oil. Fossil fuel-based plastics are not only hazardous; they’re also a finite resource. PLA products present a functional, renewable, and comparable replacement.
Bio-based – A bio-based product’s materials are derived from renewable agriculture or plants. Because all PLA products come from sugar starches, polylactic acid is considered bio-based.
Biodegradable – PLA products achieve international standards for biodegradation, naturally degrading rather than piling up in landfills. It does require certain conditions to degrade quickly. In an industrial composting facility, it can break down in 45–90 days.
Doesn’t emit toxic fumes – Unlike other plastics, bioplastics don’t emit any toxic fumes when they’re incinerated.
Thermoplastic – PLA is a thermoplastic, so it’s moldable and malleable when heated to its melting temperature. It can be solidified and injection-molded into various forms making it a terrific option for food packaging and 3D printing.
Food Contact-approved – Polylactic acid is approved as a Generally Recognized as Safe (GRAS) polymer and is safe for food contact.
The food packaging benefits:
They don’t have the same harmful chemical composition as petroleum-based products
As strong as many conventional plastics
Freezer-safe
Cups can handle temperatures of up to 110°F (PLA utensils can handle temperatures up to 200°F)
Non-toxic, carbon-neutral, and 100% renewable
In the past, when foodservice operators wanted to switch to eco-friendly packaging, they may have only found expensive and subpar products. But PLA is functional, cost effective, and sustainable. Making the switch to these products is a significant step toward reducing your food business’s carbon footprint.
Besides food packaging, what are other uses for PLA?
When it was first produced, PLA cost about $200 to make one pound. Thanks to innovations in manufacturing processes, it costs less than $1 per pound to manufacture today. Because it’s no longer cost-prohibitive, polylactic acid has the potential for massive adoption.
The most common uses include:
3D printing material filament
Food packaging
Clothing packaging
Packaging
In all these applications, the PLA alternatives present clear advantages over traditional materials.
For example, in 3D printers, PLA filaments are one of the most popular choices. They have a lower melting point than other filament options, making them easier and safer to use. 3D printing PLA filament emits lactide, which is considered a non-toxic fume. So, unlike the filament alternatives, it prints without emitting any harmful toxins.
It also presents some clear advantages in the medical field. It’s favored because of its biocompatibility and safe degradation as PLA products degrade into lactic acid. Our bodies naturally produce lactic acid, so it’s a compatible compound. Because of this, PLA is frequently used in drug delivery systems, medical implants, and tissue engineering.
In the fiber and textile world, advocates aim to replace nonrenewable polyesters with PLA fiber. Fabrics and textiles made with PLA fiber are lightweight, breathable, and recyclable.
PLA is extensively used in the packaging industry. Major companies such as Walmart, Newman’s Own Organics and Wild Oats have all begun using compostable packaging for environmental reasons.
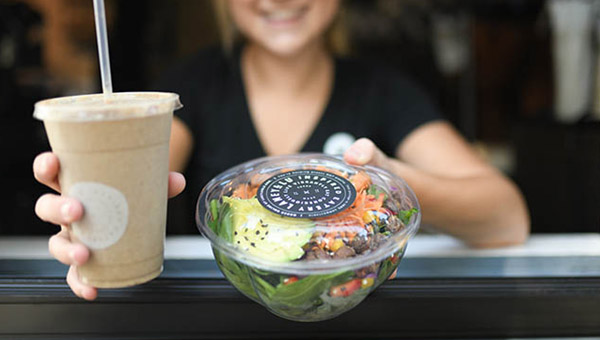
Are PLA packaging products right for my business?
If your businesses currently uses any of the following items and you’re passionate about sustainability and reducing your business’s carbon footprint, then PLA packaging is an excellent option:
Cups (cold cups)
Deli containers
Blister packaging
Food contaniers
Straws
Coffee bags
To learn more about YITO Packaging’s affordable and environmentally-friendly PLA products, get in touch!
Get free sample by williamchan@yitolibrary.com.
Related Products
Post time: May-28-2022